Engineering
"Simplicate and add more lightness"
- William Bushnell Stout
Owen Clarke have a sound background in marine, yacht, composite engineering design and materials testing. We have engineered our own designs, spars, rudder systems, foils and lifting/canting keels since our first design in 1987. When appropriate we also work with other consultant engineers on large projects and consider integrated engineering as one of the keys to a successful design, whether our own or when we’re providing consultancy services to others. An early example of our work is this FEA model and 3D design drawing of the installation of a combined lifting and canting keel system for the 20m performance cruising yacht, Spirit of Adventure. The conceptual engineering, 3D drafting and final engineering were all carried out in-house. As due diligence, the keel box and solid stainless fin were checked by an external engineering specialist using finite element analysis (FEA). The production and installation of the final component was monitored by ourselves from our Auckland office.
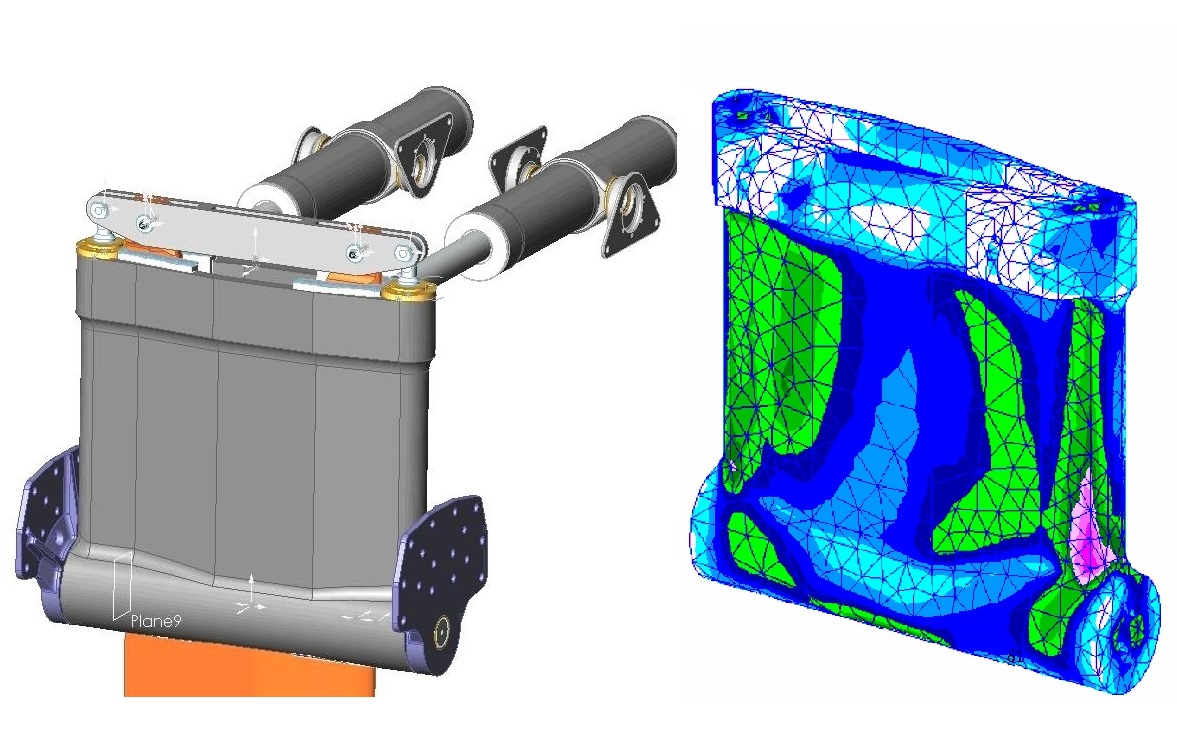
From small and seemingly insignificant items to major structures, each part is reviewed to ensure its fitness for purpose and the appropriate design and engineering methods are implemented. Designs are frequently taken from a previous project, reviewed and enhanced, or they begin life as a conceptual sketch. After this, the component is either drawn up as a two-dimensional CAD drawing, or in the case of more complex, high value or less dimensionally tolerant structures, as a three-dimensional solid model. This particular example shows the original concept sketch of the rotating bow pole for our IMOCA 60 Hexagon and the finished product which included a gennaker tack lock that OC developed for the pole end. Depending on the materials, complexity and type of part, engineering calculations are either completed by hand, via spreadsheet for the dozens of ‘standard’ components we have in our library and/or checked by FEA in house or by independent consultants.
OC have won several awards for our engineering on large sailing yacht projects, including a development of our interceptor trim control system that was retro-fitted to the 40m Wally superyacht, Angels Share. During the refit a template was made by an OC designer at the yard and the system was developed as 3D solid file, designed as a cassette to bolt precisely on the existing transom, flush to the hull with no room for error. The carbon structure and titanium alloy components were manufactured in New Zealand, then shipped to the yacht towards the end of its refit at Lurssen’s yard in Germany and fitted perfectly. In a similar example of transferable engineering design, OC developed two 6m long, 250kg carbon fibre foils for the super maxi ketch Mari Cha 4. The foils and their boxes were built in Cherbourg before being shipped to Southern France for installation. With only a few days for sailing trials the yacht left for the USA and then re-crossed the Atlantic breaking the west to east record.
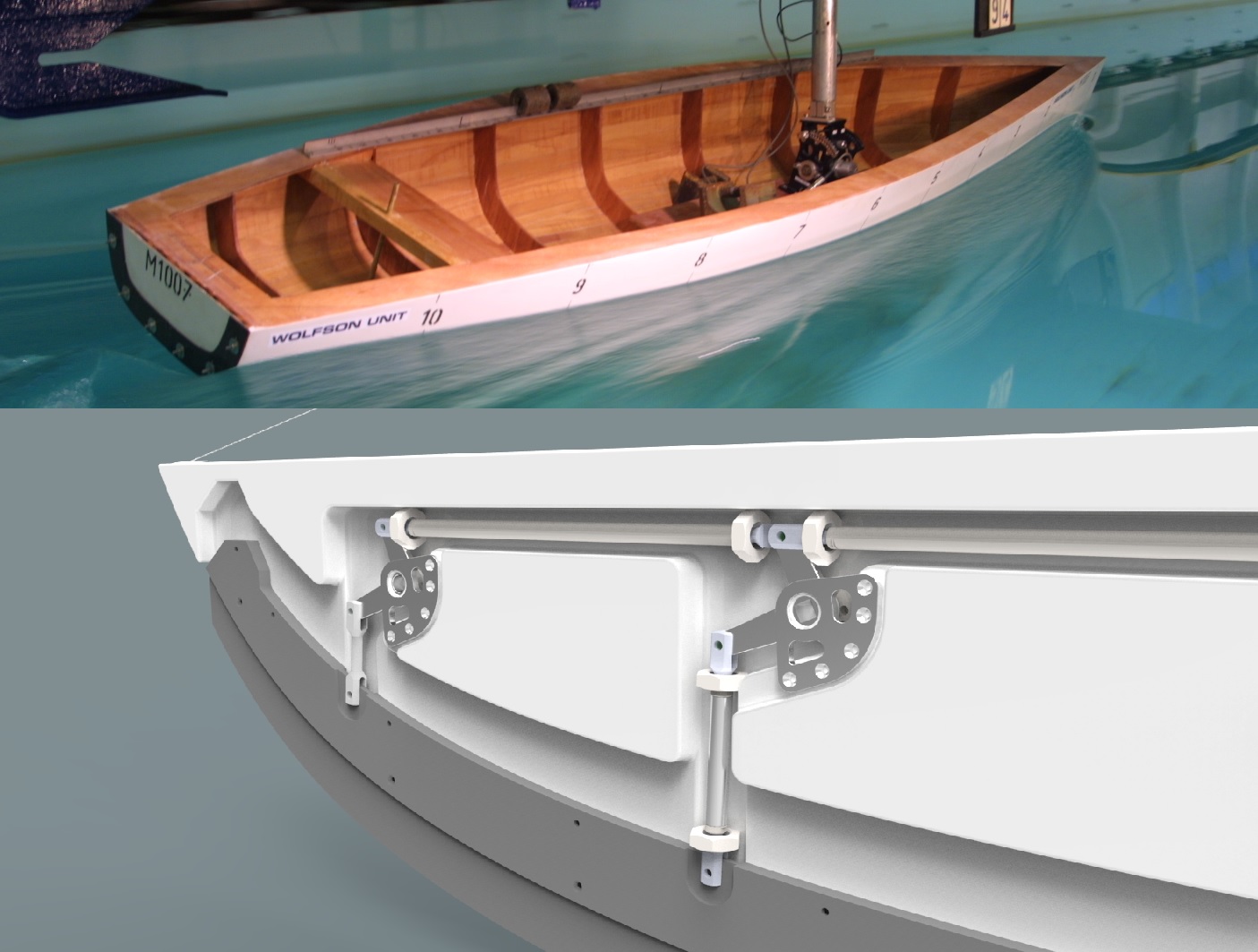
Designing custom components in 3D ensures those parts are fully optimised in terms of geometry, ensures their weight is accurately accounted for and reduces the manufacturing costs, particularly of multiple parts. An excellent example of this is the original 2D design of a ballast valve and scoop for an open 60 that was custom designed because off the shelf versions were heavy, resulted in poor (slow) flow and could not be dismantled at sea to clear blockages. The basic valve design was improved such that two tanks fore and aft in the yacht can be filled/emptied using one component saving the weight of two valves and halving the number of holes in the hull. The new design was created as a 3D solid model for CNC production purposes and the latest versions now have an even lighter composite body. Five different sized valves have been manufactured for Open 40’, 50’, 60’, Volvo 70 and maxi designs. The design is available under licence or can supplied as a finished and inspected product.
Owen Clarke undertake engineering for complete yachts and components and have experience of metals, carbon, Kevlar, glass foam, honeycomb and cedar cored structures. As well as engineering our own multihull and monohull designs etc. OC also offer engineering consultancy services to other design offices and shipyards. As consultants, specialists in foils we have completed rudders for both cruising and racing yachts between 10m and 35m, the majority of these have been certified either by IMCI or GL. OC also complete engineering inspections, act as expert witness and consultants for third parties. With large or grand prix projects where an extended team is needed, we maintain a close involvement with the engineering design while sub-contracting the primary engineering. OC continually push design boundaries in order to improve performance and reliability, part of that effort involves working with the most experienced and talented engineers in a particular area or boat type.
A strength of our office is a history of delivering complex projects that work, completed on time and to budget. Our ability to deliver comes from our background as boatbuilders, project managers, but also as mechanical engineers and designers of IMOCA 60s. By their very nature 60s include complex mechanical systems and hardware such as, canting keels and deploy systems for highly loaded foils. Our competence in mechanical design allows us to innovative in-house solutions that help to drive the rest of the design space forward and produce a better overall design. From Acciona, the first emissions free IMOCA 60 to the hybrid drive on our 25m polar motor-sailer, OC’s appliance of current and future technology leads to better solutions. We’ve taken on projects such as a three mast 75m schooner confident we can complete the mission. Our history means we always have performance and reliability in mind, whether on the race course or for example looking to reduce vibration or improve air movement in a large yacht. We really never do forget the maxim; simplicate and add more lightness.
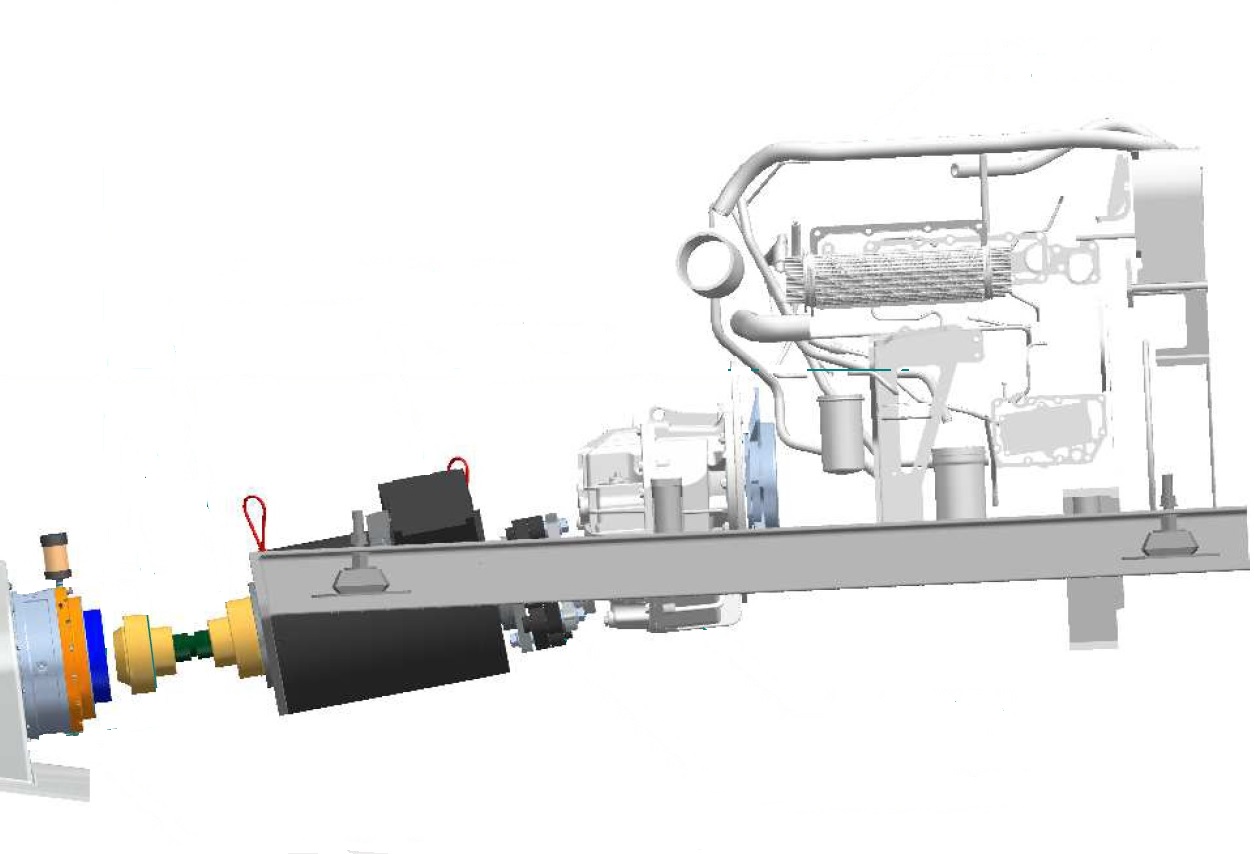
For information on other services we offer go to:
NAVAL ARCHITECTURE
For an overview of services we've provided on past projects go to:
CONSULTANCY
|